Discover What is Porosity in Welding and Its Impact on Structural Integrity
Wiki Article
Comprehending Porosity in Welding: Checking Out Reasons, Impacts, and Avoidance Techniques
Porosity in welding is a consistent difficulty that can considerably affect the quality and integrity of welds. As specialists in the welding sector are aware, comprehending the causes, results, and avoidance techniques related to porosity is crucial for attaining robust and reputable welds. By delving right into the source of porosity, analyzing its harmful results on weld top quality, and checking out effective avoidance methods, welders can enhance their expertise and skills to generate top notch welds regularly. The intricate interaction of elements adding to porosity requires a thorough understanding and a positive approach to make sure effective welding results.Usual Reasons For Porosity
Contamination, in the form of dirt, oil, or rust on the welding surface, produces gas pockets when warmed, leading to porosity in the weld. Incorrect shielding happens when the securing gas, typically made use of in processes like MIG and TIG welding, is not able to fully secure the liquified weld pool from responding with the bordering air, resulting in gas entrapment and subsequent porosity. Furthermore, inadequate gas protection, usually due to incorrect circulation prices or nozzle positioning, can leave parts of the weld vulnerable, permitting porosity to create.Effects on Weld High Quality
The presence of porosity in a weld can significantly compromise the overall quality and honesty of the bonded joint. Porosity within a weld produces spaces or tooth cavities that compromise the framework, making it much more at risk to splitting, deterioration, and mechanical failure.In addition, porosity can hinder the performance of non-destructive testing (NDT) strategies, making it challenging to spot various other flaws or discontinuities within the weld. This can bring about substantial safety and security worries, particularly in crucial applications where the structural honesty of the bonded components is paramount.
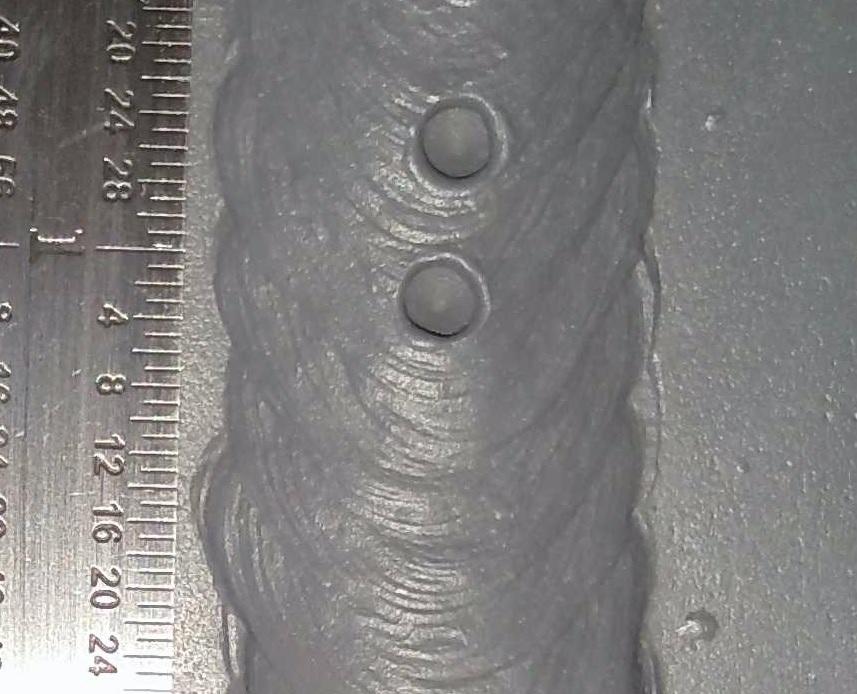
Avoidance Techniques Introduction
Offered the destructive effect of porosity on weld quality, effective avoidance methods are essential to maintaining the architectural stability of welded joints. In addition, picking the proper welding specifications, such as voltage, current, and take a trip speed, can help decrease the danger of porosity development. By integrating these prevention strategies right into welding practices, the event of porosity can be substantially reduced, leading to more powerful and much more reliable bonded joints.Importance of Correct Shielding
Correct shielding in welding plays an essential function in protecting against atmospheric contamination and making certain the stability of bonded joints. Shielding gases, such as argon, helium, or a blend of both, are commonly utilized to protect the weld pool from responding with components in the air like oxygen and nitrogen. When these responsive reference components enter into call with the warm weld pool, they can trigger porosity, bring about weak welds with reduced mechanical residential or commercial properties.Inadequate shielding can lead to different problems like porosity, spatter, and oxidation, endangering the structural stability of the welded joint. Adhering to proper securing techniques is important to create high-grade welds with minimal problems and ensure the longevity and dependability of the welded elements.
Monitoring and Control Approaches
Exactly how can welders successfully check and manage the welding process to ensure ideal outcomes and stop issues like porosity? One key technique is with making use of innovative surveillance innovations. These can include real-time tracking systems that provide comments on parameters such as voltage, existing, travel speed, and gas circulation rates. By continually keeping track of these variables, welders can recognize discrepancies find out here from the ideal problems and make prompt adjustments to stop porosity formation.
Furthermore, applying correct training programs for welders is important for keeping an eye on and managing the welding procedure properly. What is Porosity. Enlightening welders on the importance of maintaining constant criteria, such as proper gas protecting and travel speed, can help prevent porosity problems. Routine evaluations and accreditations can likewise ensure that welders excel in surveillance and regulating welding procedures
Moreover, using automated welding systems can improve tracking and control capabilities. These systems can precisely regulate welding criteria, lowering the probability of human mistake and guaranteeing constant weld quality. By incorporating innovative tracking technologies, training programs, and automated systems, welders can effectively check and regulate the welding process to minimize porosity issues and accomplish premium welds.
Conclusion
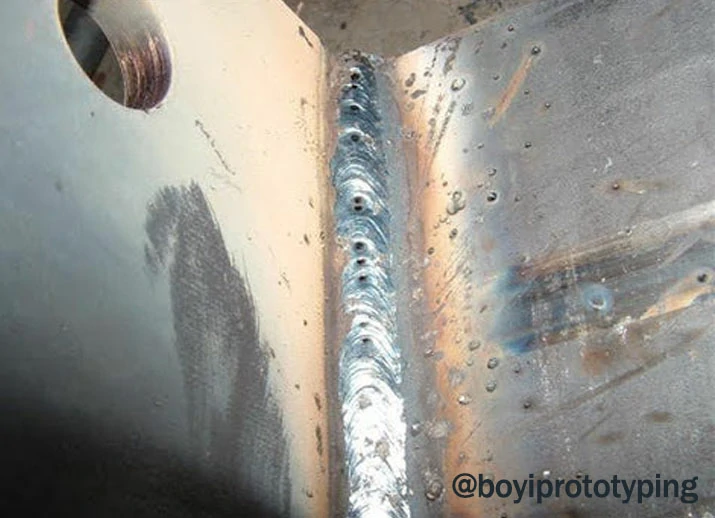
Report this wiki page